Measuring Gas Fluxes in a Flask System with the LI-8250 Multiplexer
Printable PDF: Measuring Gas Fluxes in a Flask System with the LI-8250 Multiplexer
(8250_AppNote_FlaskSamplingKit_19810.pdf)
Download this content as a pdf file.
The LI-8250 Multiplexer system is typically used to measure fluxes of trace gases from soil in situ with actuated chambers. However, with the Flask Sampling Kit (8250-660), the system can be adapted to measure gas fluxes from discrete samples, such as soil samples, fruits, or small animals, in non-actuated, user-designed chambers, referred to as flasks.
Flask Sampling Kit
LI-COR offers a flask sampling kit for integrating your LI-8250 Multiplexer into a flask system. Any LI-8250 Multiplexer or 8250-01 Extension Manifold connected to a flask must have a flask kit installed. Here are the components in the Flask Sampling Kit.
Description | Quantity | Part # |
---|---|---|
Thermistor input module | 1 | 9982-079 |
Purge pump | 1 | 9982-077 |
Purge pump mount | 1 | 9882-042 |
Bev-A-Line® tubing (15 m) | 2 | 8150-250 |
M3-0.5×6 mm mounting screw | 10 | 150-14477 |
M3-4.5×14 mm standoffs | 4 | 161-18848 |
Seal washer | 20 | 167-07256 |
Quick-connect bulkhead (female) | 8 | 300-07126 |
Quick-connect bulkhead (male) | 8 | 300-07127 |
Barbed quick-connect plug (male) | 16 | 300-07124 |
Barbed quick-connect plug (female) | 16 | 300-07125 |
Quick-connect plug | 1 | 300-08151 |
Quick-connect fitting | 2 | 300-08251 |
3/32" hex wrench | 1 | 610-04290 |
Additional Components | ||
Thermistor assembly (15 m) | optional | 9982-081 |
AC-to-DC power supply (one for each kit; one included with the LI-8250 multiplexer) | 8250-772 |
The Flask Sampling Kit contains two major components: a thermistor input module (part number 9982-079) and a purge pump (part number 9982-077). The thermistor input module allows thermistors to be attached directly to the LI-8250 Multiplexer or an 8250-01 Extension Manifold to measure air temperature inside the flasks. The purge pump serves to continuously flush the flasks with ambient (or user-conditioned) air between observations, providing a pneumatic analog to an actuated chamber.
The purge pump connects directly to the valve manifold providing flow from the instrument. The normally open side on the return manifold is left open as a vent (see Figure 1). The unpowered valves connect the normally open channel of each manifold to the pneumatic connections on the side of the instrument, such that the flow from the purge pump is divided over all inactive ports (green arrows) and isolated from the active port (blue arrows).

Figure 2 shows what happens to flow and gas concentrations for a single flask over the course of multiple sampling sequences. When the sequence is inactive and no observations are being made on any port (e.g., between the dashed and solid black vertical lines), the total purge flow is divided over all eight ports.
Once the sequence starts (solid black vertical line) and an observation is being made on one port, the purge flow increases slightly as it is now only being divided over seven of the eight ports. In both cases, the flask is in an open loop and the concentration inside the flask is relatively constant and relatively close to the concentration of the purge air.
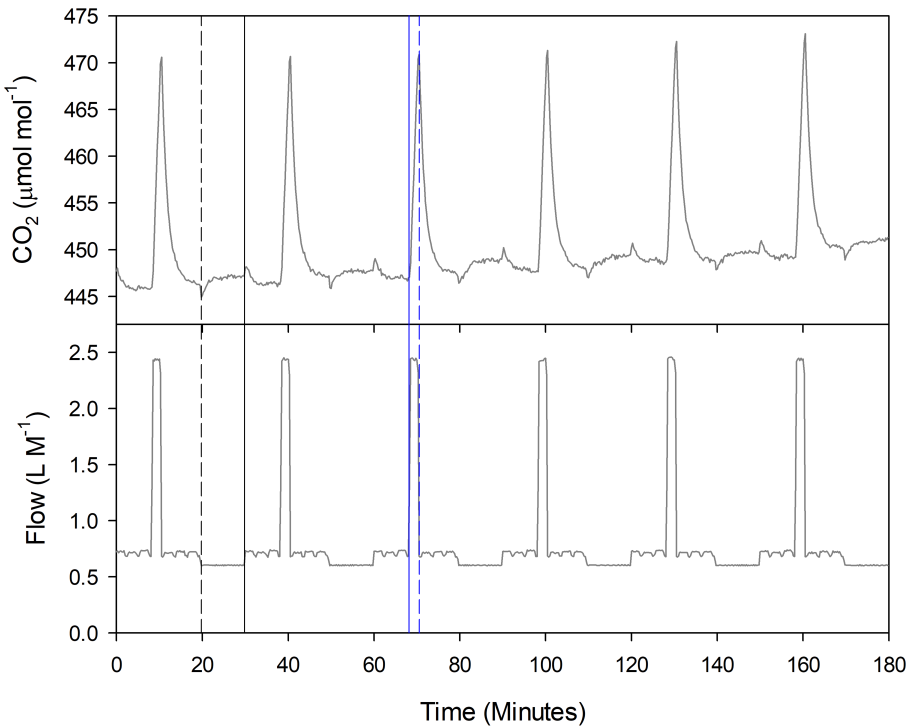
When the flask is being sampled (e.g., between the solid and dashed blue vertical lines), flow increases significantly as the flask is now the active port receiving flow from the pump. At this point, the flask is in a closed loop with the measurement system. The concentration over time will change proportional to the flux. In the example shown in Figure 2, the sample is evolving CO2 and CO2 concentration increases during the observation.
When the observation ends (dashed blue vertical line), the flask is purged and the concentration returns to the pre-observation levels. Note that the concentration does not instantly return to the pre-observation level. There is some wash out period primarily governed by the flask headspace volume and the purge flow rate. If perfect mixing in the flask is assumed, this washout time can be described by a time constant, τ:
1
Where Vh is the headspace volume and Uv is the volumetric flow rate while purging, both with matching volume units. One τ is the time it takes to achieve ~ 63% of the concentration change. For a well-mixed headspace volume, at least three times τ is required to return to the pre-observation state. For the example data in Figure 2, the headspace volume was approximately 1.6 L and the purge flow after the observation was approximately 0.7 L M-1, suggesting that it should take at least 6.8 minutes for the headspace to return to the pre-observation concentration, which fits the observed data well.
Because a flask needs to return to pre-observation conditions before another observation can be made, this time determines the minimum time between repeat observations on a flask. Depending on the nature of the sample material in the flask, some additional time may be required to allow the sample material to re-equilibrate with the headspace.
Flask design considerations
The LI-8250 Multiplexer uses a closed transient method for flux measurements. A fixed volume of air is circulated between the flask and gas analyzer(s). As the sample interacts with the air in this volume, gas concentrations change proportionally to the flux into or out of the sample and the volume. In a closed system, the flux velocity for a particular gas species is given by:
Where f is the flux velocity in mol s-1, P is pressure in Pa, Vs is system volume in m3, R is the ideal gas constant (~8.314 Pa m3 k-1 mol-1), and T is temperature in K. dc'/dt is the rate of change in the dry mixing ratio of the gas species of interest in mol mol-1 s-1.
Flux velocity is standardized by the sample surface area (s in m2) or the sample mass (g in kg), to yield an area-based flux (Fs) in mol m-2 s-1 or a mass-based flux (Fg) in mol kg-1 s-1:
3
4
Flask volume
Volume, or particularly the volume-to-unit standardization ratio (V:US), should be considered carefully in the context of expected flux rates when constructing a flask. As the volume increases for a given unit standardization and a given flux, the observed dc'/dt will decrease. With a very large flask relative to a very small flux, it is quite possible to drive dc'/dt well below the peak-to-peak noise for the analyzer used to make concentration measurements. In this case, long observation times will be required to make a measurement and uncertainty in the final computed flux will be high.
A simple sensitivity analysis using equation 2 should be done to optimize the V:US, based on expected minimum and maximum fluxes and the precision of the gas analyzer. The goal is to ensure that for the selected flask volume and expected sample area or mass, dc'/dt for the minimum expected flux is sufficiently large relative to the analyzer’s peak-to-peak noise and that the headspace concentration at the end of the observation for the largest expected flux is below the analyzer’s maximum detection limit.
Air mixing
Volume (and flask shape to some degree) is also important for turbulent mixing within the headspace. A measurement inherently assumes that the gas sample pulled from the headspace and routed through the LI-8250 Multiplexer to the gas analyzer, is representative of the conditions in the flask at the moment the sample is pulled. If the headspace volume is well mixed, this assumption is valid and the observed gas concentration will change predictably as a function of the sample flux rate.
If mixing is poor, the observed gas concentration will change, at least partially, independently of the sample flux. This may appear as oscillations or sudden steps in the observed gas concentration during the observation. Or it may simply cause erroneous measurements that represent the combined effects of the sample flux and diffusion into or out of pockets of air trapped in the headspace that are at a different concentration than the bulk air.
In general, conditions are favorable for mixing when the headspace is turbulent and few flow obstructions are present in the flask. When flow from the LI-8250 Multiplexer drives turbulence in the headspace, smaller headspace volumes are more favorable for mixing. For larger or more irregularly shaped flasks, it may be necessary to include fans inside the headspace to aid in mixing.
Analyzer loop carryover
Due to the flow scheme of the LI-8250 Multiplexer (see Figure 1), a small volume of gas in the analyzer loop is carried between measurements. In both datasets in Figure 3, the carryover is evident by the small concentration step change at Elapsed Time zero. The measured concentration before this point is dominated by the gas already in the analyzer loop. After Elapsed Time zero, the measured concentration reflects what is happening in the flask. This carryover has two practical implications for measurements in the system:
- Observed gas concentrations at the very start of an observation do not necessarily represent initial headspace concentrations in the flask.
- Gas from a previous observation is carried into the current observation.
The LI-8250 Multiplexer fits an exponential model to derive the flux. For fluxes where there is strong feedback with changes along the diffusion gradient, such as with soils in situ, this model better estimates the real flux before chamber closure disturbed the diffusion gradient. The exponential model relies on measurement of ambient concentration prior to chamber closure. This is the concentration the flux is regressed to.
In a flask system, the inherent carryover means the starting concentration does not necessarily represent the initial headspace concentration in the flask. Consequently, a sudden change is often observed some time into the observation, as shown in Figure 3. If this sudden change is not accounted for, it will impact the initial gas concentration estimate and, subsequently, the derived exponential flux. Analyzer loop carryover can be accounted for by configuring a prepurge time. For details on how to configure the prepurge time, see your LI-8250 Multiplexer manual.
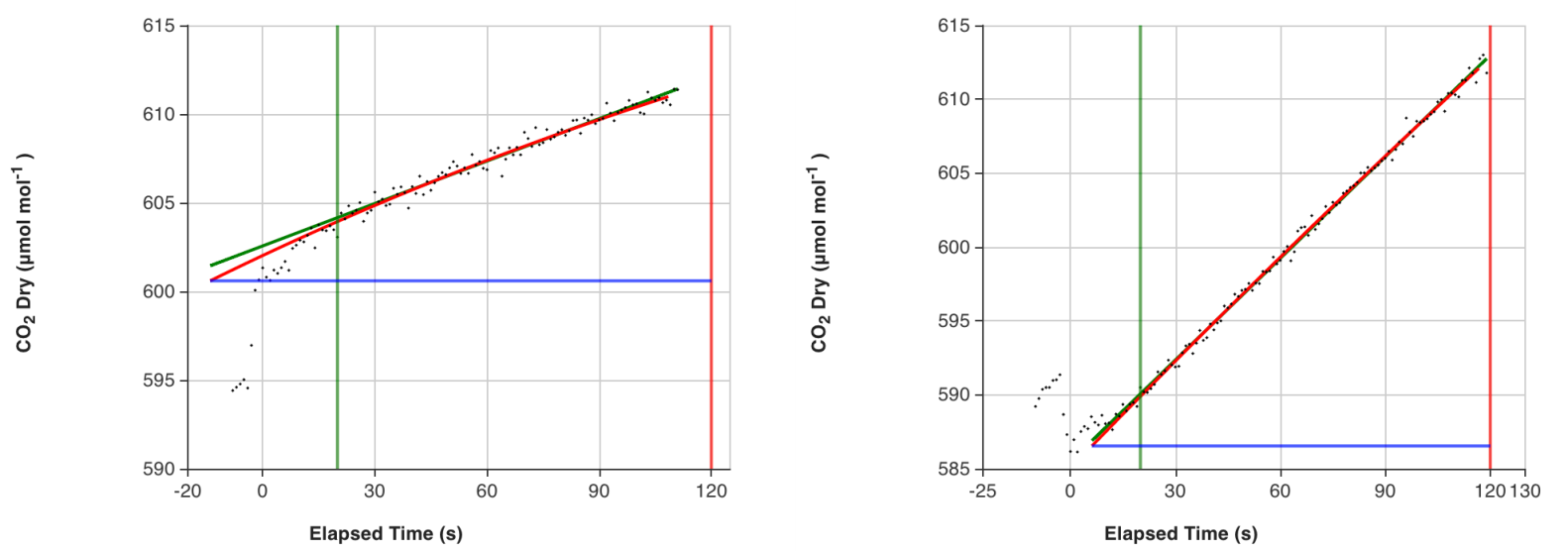
For flasks, the prepurge time is not a purging or flushing period as it is for traditional chambers. Instead, it delays the point the system considers time zero and when the initial concentration is taken (blue lines in Figure 3). In Figure 3, data was collected using a 10-second prepurge. In both cases, the result is an initial concentration estimate that fits well with the subsequent data. To determine the prepurge time, we suggest making some preliminary measurements using your specific setup before collecting any meaningful data.
Note: The prepurge is not adjustable in SoilFluxPro™ Software like the other parameters are, making it difficult to recover the correct exponential flux when using an inappropriate prepurge. SoilFluxPro fits an exponential and linear model with a flux estimate from both. The linear model is mostly unaffected by prepurge time, meaning the linear flux can often be used to get a flux estimate for data collected with an inappropriate prepurge.
For studies where mixing of gas between flasks is undesirable, a port can be dedicated as an analyzer loop purge. This will flush the analyzer loop with ambient (or user-conditioned) air between observations and will greatly reduce or eliminate flask-to-flask gas mixing. However, the air in the analyzer loop from the purge will still be carried over to the next flask observation.
Hardware requirements
Both the purge pump and thermistor input module are required for flask measurements, and both must be installed in any instrument (LI-8250 Multiplexer or 8250-01 Extension Manifold) that connects to a flask. For example, if you have a system with a multiplexer and two extension manifolds and you would like to connect flasks to each, three flask kits are needed (one for each instrument). If, for example, you will not be connecting any flasks to the multiplexer, only two flask kits are needed (one per extension manifold).
Because the current draw for a purge pump in an extension manifold exceeds what the multiplexer can supply, each extension manifold used for flask measurements must be powered via the alternate power input. You will need one indoor AC to DC power supply (part number 8250-772) for each extension manifold with a flask kit. You can power the multiplexer using the indoor AC to DC power supply or the outdoor AC to DC power supply (part number 8250-770).
Flask measurements require at least one temperature measurement. The temperature measurement must be made using a thermistor connected to the same instrument as the flask. Up to eight thermistors can be connected to each thermistor input module, and a thermistor can be mapped to one or more flasks.
In our example system above, if flasks are connected to the multiplexer and both extension manifolds, a minimum of three thermistors are required (one per instrument). If each flask had a thermistor, there could be up to 22 thermistors (eight on each extension manifold and six on the multiplexer). Where temperatures are relatively uniform across the system, such as in a temperature-controlled growth cabinet, one thermistor per instrument may be sufficient. Where temperatures differ across the system, multiple thermistors will be required.
Preassembled, weatherized thermistors are available from LI-COR (part number 9982-081). These thermistors are potted into a stainless-steel housing, fit to a sealed cable gland, and include a 15 m shielded cable. The cable gland mounts through a 12.5 mm diameter hole in materials up to 3 mm thick and is held in place by a nylon hex nut. Alternatively, the gland may be threaded directly into a PG 7 (steel conduit threading per DIN 40430) threaded hole.
Note: For a proper seal, the gland shoulder must compress against the mounting surface, where the gasket is located.
User-provided thermistors can also be used in the system. The thermistor input module is optimized for 10 kOhms at 25 °C nominal NTC thermistors. Steinhart-Hart coefficients for the user-provided thermistor must be known and set in the instrument configuration. No provision is included in the flask kit to seal a user-provided thermistor into a flask.
Pneumatic connections
Each Flask Sampling kit includes fittings and 30 m of Bev-A-Line® tubing to connect the user flask to the instrument (see Figure 4). You may cut the tubing to your desired length, and additional tubing can be ordered in 15 m rolls using part number 8150-250.
The tubing connects to fittings installed on the flask and to the instrument using barbed quick-connect fittings (part numbers: 300-07124 [male] and 300-07125 [female]). These fittings have a barb on one side that you press into the end of the tubing. Ensure you have cut the tubing end square and cleanly before inserting the barb. Install one male and one female barbed quick-connect fitting per tube.
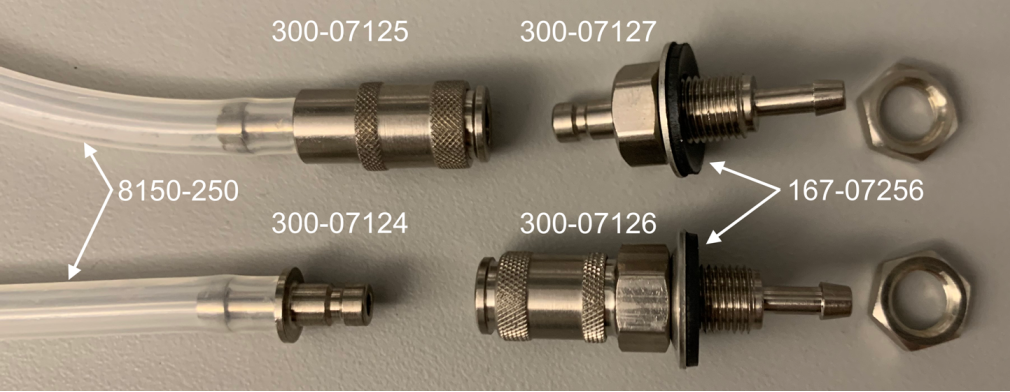
Bulkhead quick-connect fittings (part numbers: 300-07126 [female] and 300-07127 [male]) provide a connection at the flask. These fittings mount through materials up to 4.5 mm thick (accounting for seal thickness) via an 8.5 mm diameter through-hole. Seal washers (part number 167-07256) provide a gas-tight seal. Slide the washer over the threads of the fitting with the rubber side away from the quick-connect end. Install one male and one female bulkhead quick-connect fitting per flask using an 11 mm wrench for the fittings and accompanying nuts.
Note: To properly seal, the rubber side of the washer must compress against the mounting surface.
An example flask system used to measure soil CO2 and CH4 fluxes
An example flask system was set up using an LI-8250 Multiplexer, an LI-7810 CH4/CO2/H2O Trace Gas Analyzer, and seven flasks. The flasks were constructed from 2 L, wide mouth Mason jars. Lids for all flasks were fitted with quick-connect bulk heads and connected to the multiplexer with 1.5 m lengths of Bev-A-Line® tubing. Lids for five of the flasks were also fitted with thermistor assemblies (part number 9982-081). The remaining two flasks were mapped in software to thermistors in flasks on adjoining ports. The remaining multiplexer port was left open to serve as an analyzer loop purge.
A clay-loam soil was collected from an agricultural site in Lincoln, NE. The soil was sieved to homogenize it and remove coarse materials > 2 mm. Approximately 250 g dry weight equivalent of the homogenized soil was placed in six of the flasks. One flask was left empty to serve as a zero-flux reference. On the fourth day after placing the soil samples in the flask, 50 ml of water was added to all flasks containing soil. Three of these flasks were also dosed with 3.5 g of sucrose dissolved in the water.
Gas fluxes were measured sequentially on all seven flasks at half-hour intervals. Observations were made over a 120-second period preceded by a 10-second prepurge. Between each observation on a flask, the analyzer loop purge port was sampled for 30 seconds.
CO2 fluxes from all flasks containing soil (ports 1, 2, 3, 5, 6, and 7) were quite similar prior to the water and water plus sucrose additions and were distinct from the zero-flux measured with the empty flask (port 8) (see Figure 5).
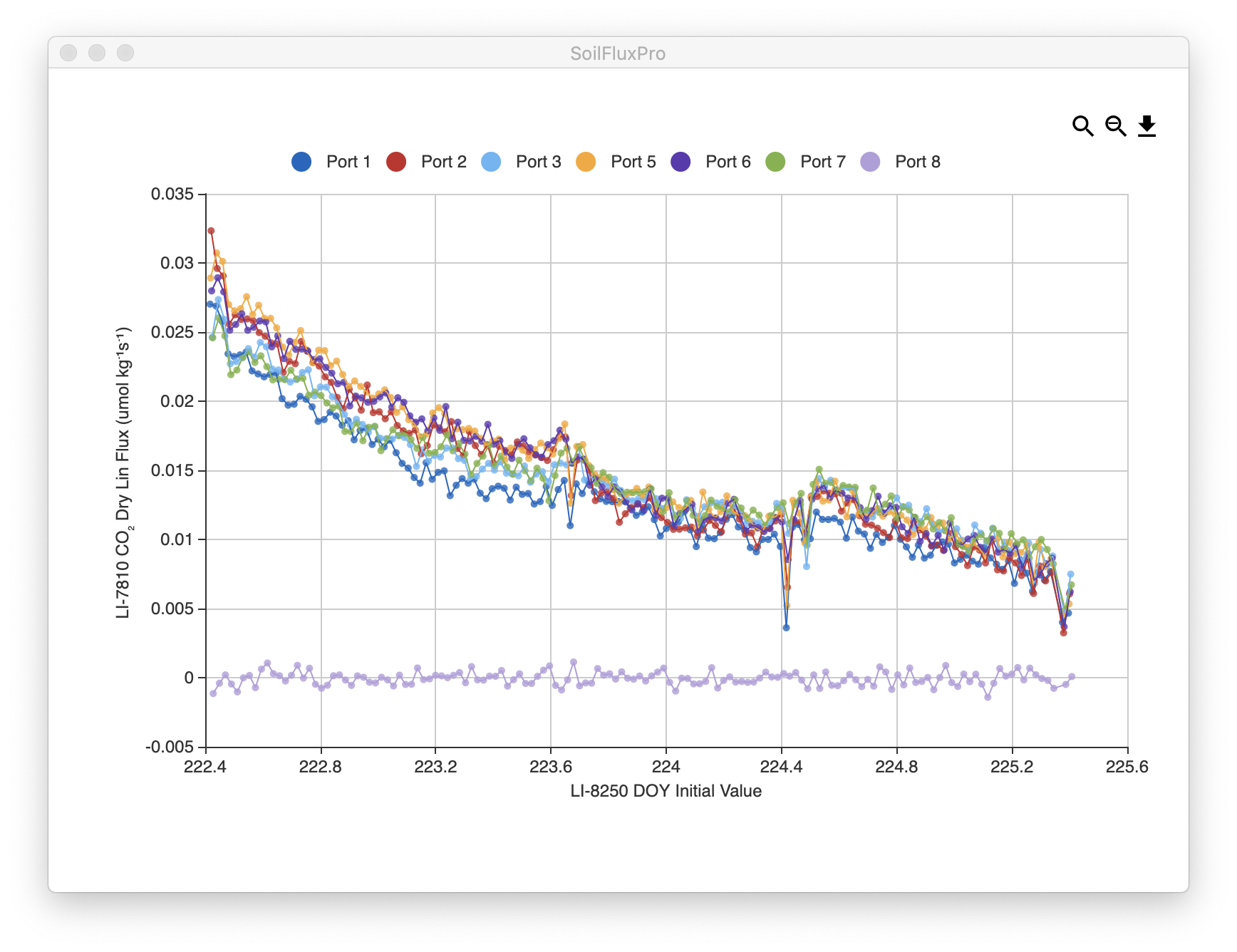
The addition of water to all flasks caused some increase in the observed CO2 flux, however, this increase was small compared to the increase driven by including sucrose (ports 5, 6, and 7 included sucrose) (see Figure 6).
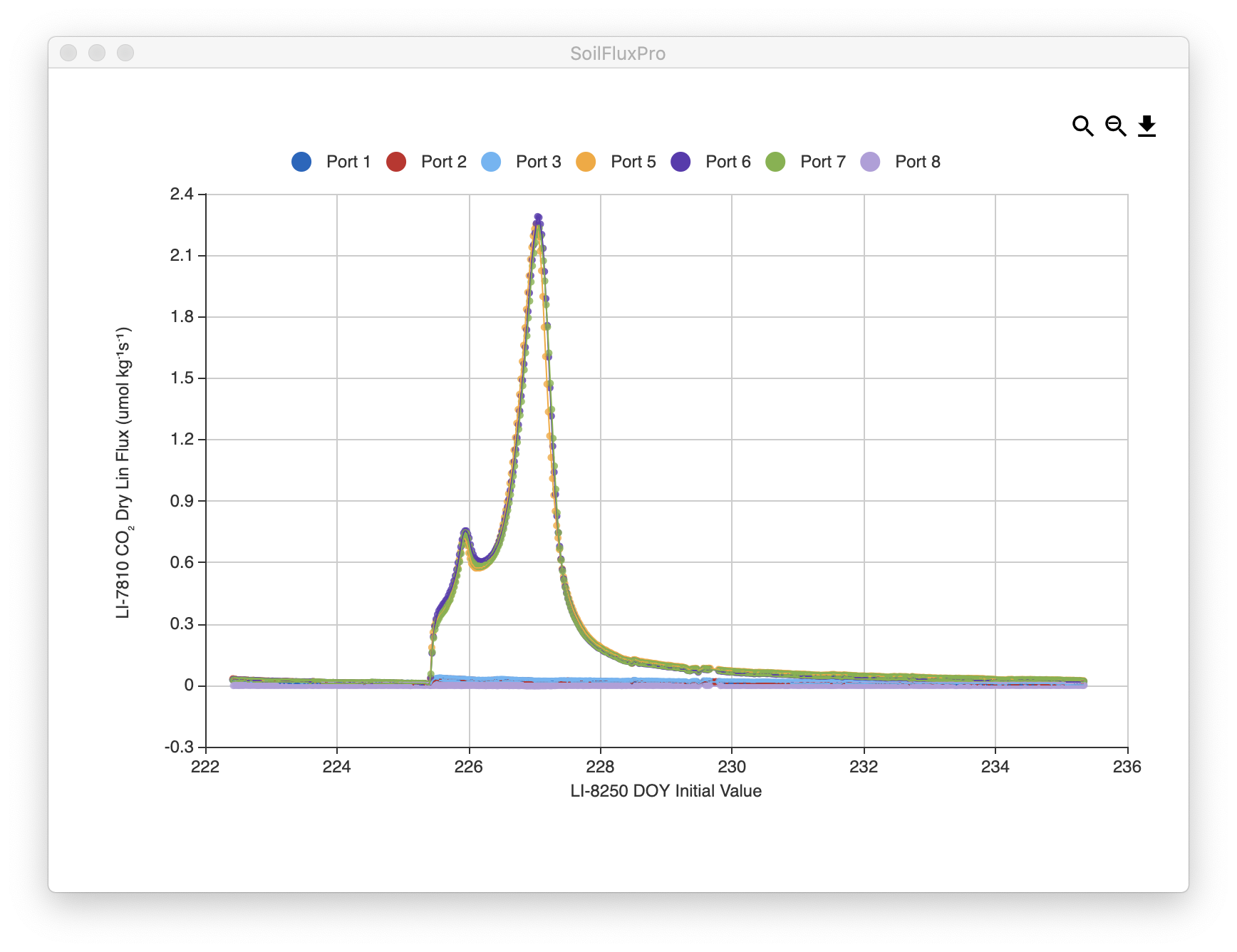
CH4 fluxes were mostly similar across all flasks for the duration of the measurement period and were rarely different than the zero-flux measured with the empty flask (see Figure 7). Where a non-zero CH4 flux was observed, it seems driven primarily by the soil sample pore spaces coming into equilibrium after large diurnal swings in the ambient CH4 concentration.
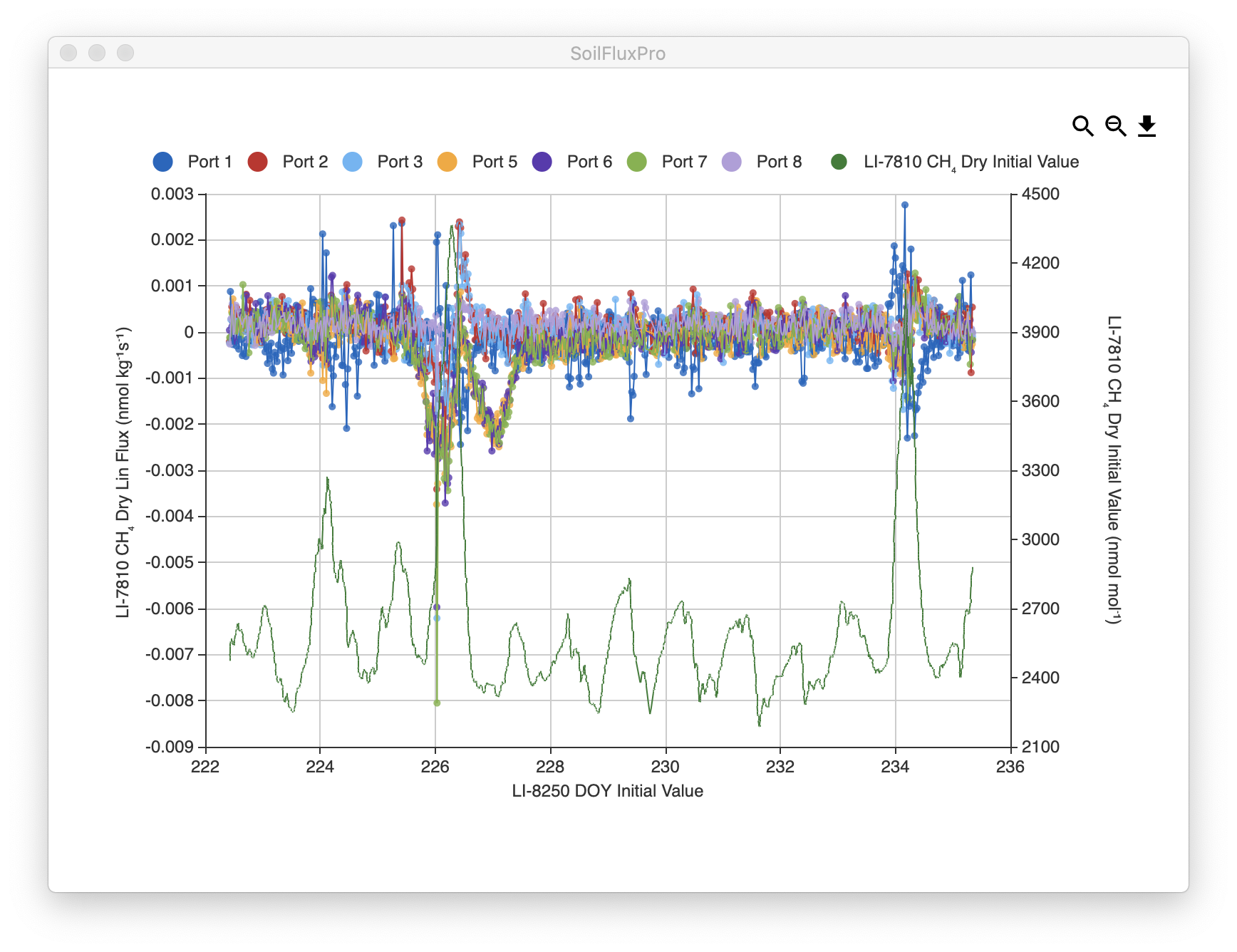